洁净区受控环境的质量把控:关键要素与管理实践
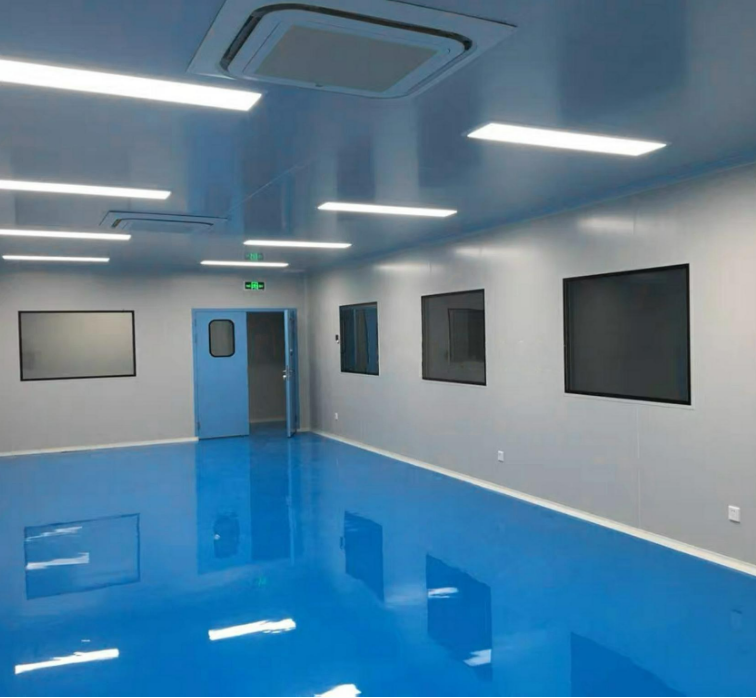
一、洁净区环境质量的核心控制要素
1. 空气洁净度等级控制
国际标准依据:根据ISO 14644-1标准,洁净区按空气中悬浮粒子浓度划分为ISO 1至ISO 9等级(如制药行业常用ISO 5级,对应百级洁净区)。
动态与静态控制:
静态:设备运行但无人员操作时的洁净度;
动态:正常生产状态下的洁净度(需预留安全余量)。
2. 温湿度与压差管理
温度:通常控制在18~26℃(根据工艺需求调整);
湿度:一般要求45%~65%(防止静电或微生物滋生);
压差梯度:相邻洁净区压差需≥5Pa,确保气流从高洁净区流向低洁净区。
3. 微生物污染防控
通过高效空气过滤器(HEPA)去除空气中≥0.3μm的微粒;
定期进行沉降菌、浮游菌检测(如《中国药典》要求)。
二、洁净区环境质量的管理体系
1. HVAC系统的设计与验证
空气处理系统:采用三级过滤(初效+中效+高效),确保换气次数达标(如ISO 5级需≥240次/小时);
验证流程:安装确认(IQ)、运行确认(OQ)、性能确认(PQ),定期再验证。
2. 实时监测与数据追溯
在线粒子计数器:连续监测空气中粒子浓度并报警;
环境监控系统(EMS):整合温湿度、压差、粒子数据,实现电子化记录与趋势分析。
3. 人员行为规范
更衣程序:严格遵循“一更→二更→缓冲”流程,使用无尘服及手套;
操作限制:禁止跑动、大声交谈,限制同时进入人数;
培训考核:定期开展洁净区SOP(标准操作规程)培训。
三、常见风险与应对策略
1. 微粒污染风险
来源:设备磨损、人员活动、物料带入;
控制措施:
采用不锈钢材质设备,减少脱落微粒;
物料经传递窗消毒后进入洁净区。
2. 微生物超标问题
消毒程序:
每日使用75%乙醇或过氧化氢对表面擦拭消毒;
每月交替使用不同种类杀孢子剂。
环境监测频率:关键区域(如灌装线)每小时监测,普通区域每日监测。
3. 系统故障应急响应
制定《洁净区环境异常处理预案》,明确压差失衡、空调停机等情况的处理流程;
备用电源(UPS)保障关键设备持续运行。
四、持续改进与合规性管理
1. 数据驱动的质量分析
通过EMS系统统计历史数据,识别季节性或周期性波动;
采用统计学工具(如六西格玛)优化控制参数。
2. 法规符合性
遵循GMP(药品生产质量管理规范)、FDA 21 CFR Part 11(电子记录要求)等法规;
定期接受第三方审计,确保体系有效性。
3. 技术创新应用
引入物联网(IoT)传感器实现远程监控;
应用单向流(层流)技术保护关键操作区域。
五、案例分析:某药企A级洁净区的优化实践
背景:某企业无菌灌装线多次检测到微生物临界偏差。
改进措施:
升级HVAC系统末端高效过滤器(H14→U15);
实施人员模拟操作考核,降低动作幅度;
引入快速微生物检测技术(如ATP生物荧光法)。
结果:微生物合格率从92%提升至99.5%,偏差事件减少80%。
洁净区环境的质量把控是一项系统性工程,需融合硬件设计、智能监控、人员管理和持续改进。只有通过科学的风险评估和全生命周期管理,才能实现从“符合标准”到“质量卓越”的跨越,为高附加值产品的生产提供可靠保障。
是否对此产品感兴趣